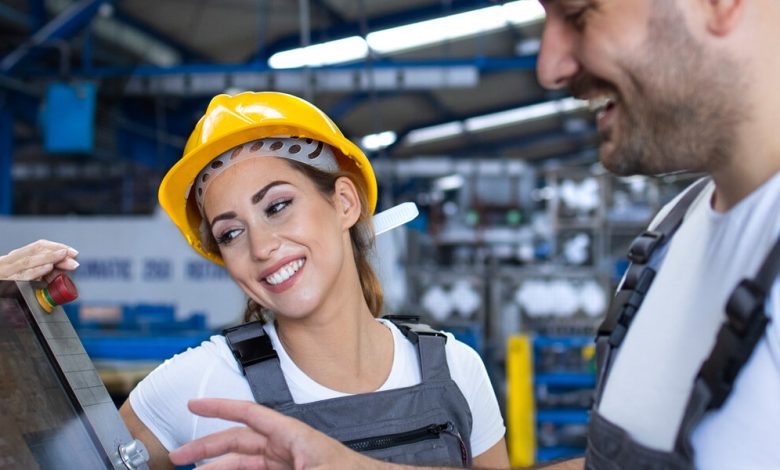
Automated material handling systems guarantee that material transports efficiently from one location in the manufacturing area to another. Whether it’s within the same department or bay, on opposite sides of the factory floor, or even in two different buildings.
The way we manage resources, orders, and packaging in today’s demanding and busy world must be efficient and very optimized. End consumers are wanting greater value, faster delivery, and excellent quality for their money. Many businesses need to step up their game with more efficient technology, improved space, and effective warehousing systems to satisfy these expectations.
What Are Automated Material Handling Systems, and How Do They Work?
Instead of human labor, Automated Material Handling Systems employ digital devices and robots to transport, lift, pull, push, store, and retrieve things. Heavy equipment box lifts, conveyors, pallet lifting devices, and industrial lifting devices are just a few examples.
Automated material handling systems have begun to be recognize by several sectors. While automated technology may considerably increase warehouse efficiency, you must consider the high upfront expenses as well as the potential for unplanned downtime if a machine goes down.
What Is the Difference Between Manual and Automated Material Handling?
Human operators are required to transport products across the warehouse using manual handling methods, which may include the use of forklifts, incline conveyor belt mini cranes, hook lifters, and other tools. These installations are typically slower and take longer than automated methods. Due to the human factor, they may also result in additional mistakes and inaccuracies.
A manual handling system has a cheap initial cost, and you’ll likely get a rapid return on your investment. However, because staff will be operating the equipment directly, numerous training sessions will be require to prevent workplace injuries and mishaps.
Automated handling systems, on the other hand, can identify, transfer, collect, and store your products without the need for human interaction. As a result, they are quicker and may be programme to accomplish numerous jobs at once. Your operations, on the other hand, may come to a halt if they fail.
Automated material handling systems are precise and scalable, but they need significant investment and take longer to pay off. In addition, competent operators will be require to program and operate the various machines. These drawbacks, however, are minor in comparison to the cost savings and increased productivity that an automated system will provide.
Material Handling Equipment: Where Is It Use And How Does It Work?
Customized material handling systems may help businesses in a variety of industries. While exact designs will differ depending on the targeted uses, all systems have the potential to increase productivity and precision.
Listed below are just a handful of the numerous industries that employ sophisticated material handling systems extensively:
Distribution Centers: Today’s distribution centers, which are among the best places to use material handling equipment, require effective technical solutions to reduce picking and packaging costs. Even in an omnichannel environment, the correct automated material handling system will enhance resource efficiency while simultaneously supporting nimble operations.
E-commerce: With each year’s record online sales, demand for automated systems is on the rise in the e-commerce business. Many businesses are deploying ASRS and other high-tech solutions to assist in speeding up the order fulfillment process in order to meet this unprecedented demand.
Automotive: In the modern automobile industry, where complicated production protocols and short product lifecycles drive a growing need for automated systems, flexible material handling solutions are critical.
Aerospace: In the rapidly changing aircraft sector, where fragile parts and stringent security measures must be considered, innovative solutions are critical. Today’s aircraft material handling systems are as sophisticated as the cutting-edge technology with which they work.
Food and beverages: When creating solutions for handling food and drinks, temperature needs and a variety of other storage factors must be taken into account. Material handling systems that are strategically plan may guarantee that items move smoothly through facilities and are easily located, reducing waste.
BENEFITS OF AUTOMATED MATERIAL HANDLING SYSTEMS:
The benefits of automated material handling systems are numerous, and their entire value and responsibility are dependent on their integration. You can combine and intermix some AMHS equipment while preserving certain manual stations, or you can build a totally autonomous automated structure based on your budget and specific demands.
Your platform will become more independent as it integrates and improves. AMHS can detect goods that have been offload by an operator, identify them, process them appropriately. Determine their next destination, and even transport them to that station. Routing, delivery, identification, handling, and everything else in between are all automated in a fully establish system.
Warehouse management is a complicated process that involves numerous processes and stations throughout the lifespan of a product or shipment. It can be incredibly costly, repetitive, sluggish, and redundant if done only by your personnel. The key benefit of using an Automated Material Handling System is that it may address all. Of these issues and provide. You with a more efficient warehouse at a lower cost.